Autorin: Maria Kaminski
#diensttalk mit Dr. Sylvia Gebhardt zu neuen Technologieansätzen für Ultraschallwandler
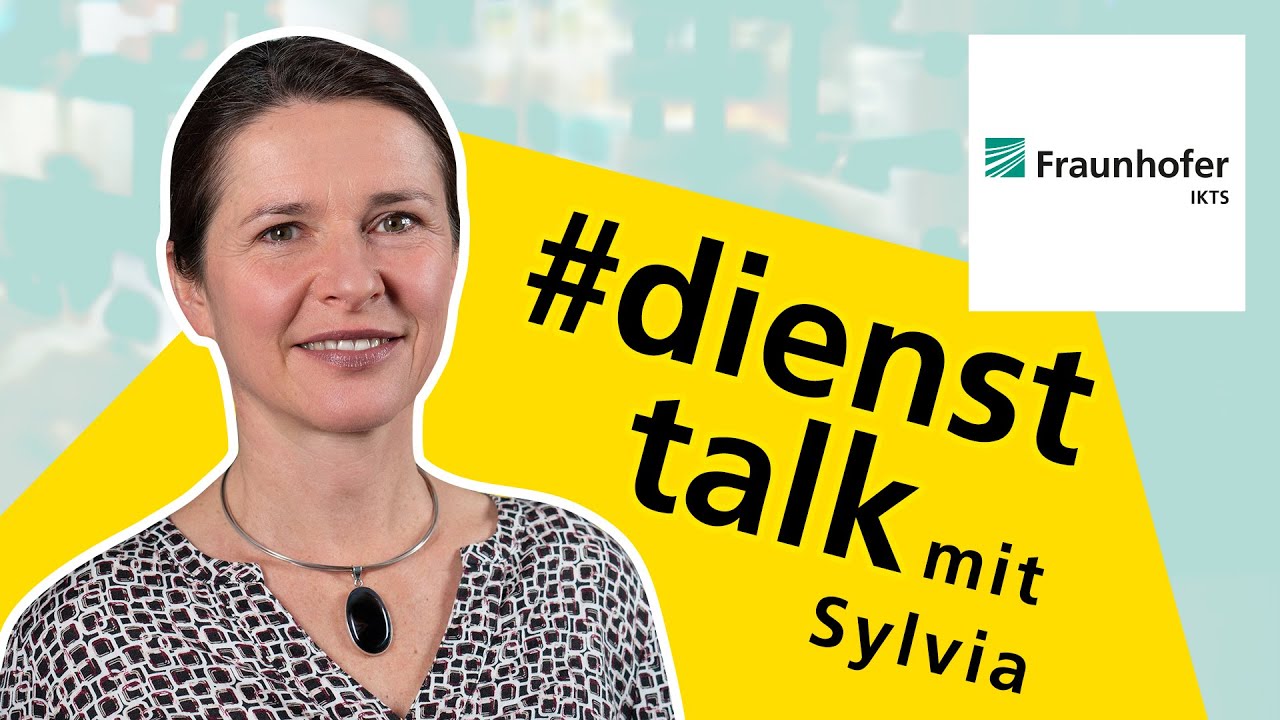
Datenschutz und Datenverarbeitung
Wir setzen zum Einbinden von Videos den Anbieter YouTube ein. Wie die meisten Websites verwendet YouTube Cookies, um Informationen über die Besucher ihrer Internetseite zu sammeln. Wenn Sie das Video starten, könnte dies Datenverarbeitungsvorgänge auslösen. Darauf haben wir keinen Einfluss. Weitere Informationen über Datenschutz bei YouTube finden Sie in deren Datenschutzerklärung unter: https://policies.google.com/privacy#diensttalk mit Dr. Sylvia Gebhardt über Funktionskeramik und die akustische Wellen.
Im Kampf um Leben und Tod zählt jede Minute. Werden Patienten direkt vor Ort, zum Beispiel nach einem Unfall, behandelt, erhöhen sich ihre Überlebenschancen erheblich. Damit Notfallmediziner schnell die richtige Diagnose stellen können, kommen u. a. mobile Ultraschallgeräte zum Einsatz. So können bereits am Unfallort notwenige Behandlungsschritte eingeleitet werden. Ultraschallgeräte werden allerdings nicht nur in der medizinischen Diagnostik eingesetzt, sondern auch bei der Bildgebung für die zerstörungsfreie Werkstoffprüfung.
Sie haben deutliche Vorteile im Vergleich zur Röntgenanalyse aufgrund ihres nicht-ionisierenden Charakters und der Tatsache, dass aus den gewonnenen Bildern und Messungen zusätzliche physikalische sowie strukturelle Informationen der untersuchten Medien abgeleitet werden können. Doch gerade dieser Miniaturisierungstrend bei den Wandlern stellt die Konstrukteure des Fraunhofer IKTS vor riesige Herausforderungen – vor allem bei der Entwicklung innovativer Fertigungsverfahren.
Das herkömmliche Herstellungsverfahren von Ultraschallwandlern besteht aus mehreren Teilschritten. Herzstück ist eine piezokeramische Platte, die auf Zieldicke abgeschliffen, beidseitig elektrodiert und gepolt wird. Anschließend wird die Platte auf einen Dämpfungskörper geklebt, gesägt und mit Anpassschichten versehen. Dieses Verfahren ist nicht nur umständlich, sondern es entstehen Klebschichten, die den akustischen Schall stören. Dieser Nachteil kann durch drucktechnische Verfahren behoben werden. Zur Herstellung anwendungsspezifischer Ultraschallwandler werden am IKTS verschiedene Druckverfahren entwickelt, die zukünftig die aufwendige Fertigung von Ultraschallwandlern über Assemblierungstechniken ablösen sollen.
Vom Siebdruck bis hin zum düsenbasierten Druckverfahren
Das Siebdruckverfahren erlaubt den Druck von Strukturen mit einer Auflösung von bis zu 100 µm und einer Dicke von 30 bis 150 µm – sogenannte Dickschichten – auf planaren und tubularen Substraten. Das Druckbild, und damit die Struktur der Ultraschallwandler, wird durch die Sieböffnung vorgegeben, durch die die Paste während des Druckprozesses gedrückt wird: das passiert nicht nur sehr schnell, sondern auch mit hoher Reproduzierbarkeit. Grundlage dafür sind piezokeramische Siebdruckpasten, wie sie am IKTS entwickelt werden. Dieses Verfahren erlaubt die Serienfertigung von Bauteilen in großer Stückzahl, ist allerdings in der realisierbaren Bauteilgeometrie begrenzt.
Komplexe Bauteilstrukturen mit Mehrfachkrümmung, wie sie z. B. für selbstfokussierende Ultraschallwandler von Vorteil sind, erfordern den Einsatz düsenbasierter Druckverfahren. Hierzu stehen am Fraunhofer IKTS der Aerosoljet-Druck und der Dispens-(Jet)-Druck zur Verfügung. Für diese Verfahren werden spezielle Tinten bzw. Pasten entwickelt, die einen düsenbasierten Auftrag erlauben. Dieser Technologieansatz ermöglicht die Realisierung wesentlich feinerer Strukturauflösungen von bis zu 40 µm bei einer Dicke von 5 bis 30 µm.
Realisierung von Ultraschallwandlern mit drucktechnischen Verfahren
Für den Aufbau der Ultraschallwandler sind mehrere Druck- und Einbrandschritte notwendig. Zunächst wird die Grundelektrode in Linien- oder Ringform aufgebracht und eingebrannt. Die laterale Abmessung der Strukturen bestimmt den Fokus der ausgestrahlten Ultraschallkeule und damit die mögliche Bildauflösung des Wandlers. Danach erfolgt der Druck der piezokeramischen Schicht. Je nach gewünschter Schichtdicke werden mehrere Druckzyklen gefahren. Im Anschluss werden sowohl Isolationsschichten für Überkontaktierungen als auch Deckelektroden- und Anpassschichten aufgedruckt.
Zukünftige Realisierung in einer Prozesskette
Ziel ist es, das ungestörte Senden und Empfangen von Ultraschallwellen zu gewährleisten. Dabei spielt die Porosität des Substrats eine entscheidende Rolle. Die gezielte Einstellung der Porosität der Substrate soll eine komplette Dämpfung des rückgestreuten Ultraschallechos und damit ein ungestörtes Senden und Empfangen von Ultraschallwellen im Frequenzbereich zwischen 5 und 40 MHz ermöglichen. Derzeit werden am Fraunhofer IKTS Demonstratoren auf Basis der Siebdrucktechnik gefertigt. So werden beispielsweise Linienwandler für die Medizintechnik aber auch Ringarrays für die zerstörungsfreie Werkstoffprüfung auf unterschiedliche Substrate gedruckt. Zukünftig sollen Dämpfungskörper, Ultraschallwandler sowie Aufbau- und Verbindungstechnik in einer Prozesskette realisiert werden. Bereits jetzt steht das Fraunhofer IKTS in engem Kontakt mit der Industrie, die die am IKTS entwickelten, gedruckten und gefertigten Wandler für die zerstörungsfreie Prüfung von Siliziumwafern in der Halbleiterindustrie sowie für die Medizintechnik einsetzen möchte.
Kostengünstige Fertigung in großer Stückzahl
Die Verwendung druckbasierter Verfahren erlaubt im Vergleich zu bisherigen Assemblierungsverfahren eine kostengünstige und zeitsparende Fertigung von Ultraschallwandlern in großer Stückzahl. Sie sind kompakt aufgebaut und entsprechen damit dem Trend zur Miniaturisierung, Preisreduzierung und elektronischen Verdichtung. Das prädestiniert sie für den Einsatz in portablen und ultra-portablen Geräten für Laptop- oder Smartphone-basierte Anwendungen.
Die gedruckten Ultraschallwandler sind zudem frei von störenden Zwischenschichten und bieten den Vorteil einer integrierten Aufbau- und Verbindungstechnik. Während die Weiterkontaktierung von herkömmlichen Ultraschallwandlern durch Verdrahtung sowie Löt- bzw. Bondkontakte erfolgt, können über Drucktechnik die Leitpfade direkt aufgebracht werden. Dies verhindert den Auftrag voluminöser Löt- bzw. Bondpads, die das Schwingungsverhalten des Wandlers negativ beeinflussen.
Einsatzfelder von der Medizintechnik bis hin zur zerstörungsfreien Prüfung
Herkömmliche Ultraschallbildgebungssysteme werden typischerweise bei Frequenzen zwischen 1 und 15 MHz betrieben. Ziel der Untersuchungen am IKTS ist die Entwicklung hochfrequenter Ultraschallwandler mit Frequenzen oberhalb von 15 MHz, um eine Verbesserung der Bildauflösung zu erreichen. Da mit steigender Ultraschallfrequenz nicht nur die Auflösung zunimmt, sondern auch die akustische Eindringtiefe ins Gewebe abnimmt, eignen sich hochfrequente Ultraschallwandler besonders für oberflächennahe oder durch Katheder erreichbare Strukturen, z. B. im Rahmen dermatologischer, ophthalmologischer oder intravaskulärer Untersuchungen. Diese Eigenschaft macht sie nicht nur für die Medizintechnik, sondern auch für präklinische Labortieruntersuchungen sowie die zerstörungsfreie Prüfung von faserverstärkten Kunststoffen, stoffschlüssigen Verbindungen und elektronischen Bauteilen in der Halbleiterindustrie interessant.
Das Projekt wurde von der Arbeitsgemeinschaft industrieller Forschungsvereinigungen Otto von Guericke e.V. gefördert.
Weiterführende Informationen:
Piezokeramische Dickschichten
Hier geht's zu weiteren #diensttalks. Blicken Sie hinter die Kulissen des Fraunhofer IKTS.
Bleiben Sie darüber hinaus informiert: Melden Sie sich gern für unseren Newsletter an, lesen Sie in weitere Blogbeiträge rein oder folgen Sie uns auf LinkedIn, Instagram und YouTube. Wir freuen uns, mit Ihnen ins Gespräch zu kommen.
