Auf dem Weg zur kostengünstigen Natriumbatterie
Der Einsatz von Natriumbatterien verspricht sowohl ökonomische als auch ökologische Vorteile. Um die Effizienz in der Herstellung des keramischen Elektrolyten weiter zu steigern, soll im Rahmen des Projekts InBatt eine Inline-Qualitätskontrolle entwickelt werden. Diese erkennt Defekte im Elektrolyten frühzeitig im Herstellungsprozess und hilft so dabei, Material, Energie und Kosten zu sparen.
Natrium-Ionen-Batterien überzeugen auf mehreren Ebenen: sie basieren auf Natriumsalzen, die gut verfügbar sowie recyclebar sind. Damit enthalten sie keine oder nur sehr geringe Mengen kritischer Rohstoffe. Das ist umweltfreundlicher und reduziert Materialkosten. Durch den Einsatz eines Festelektrolyten lassen sich im Vergleich zu herkömmlichen Zellen, die flüssige oder auf organischen Lösungsmitteln basierende Elektrolyte verwenden, hohe Energie- und Leistungsdichten sowie eine außergewöhnliche Sicherheit erreichen. Die Herstellung dieser Elektrolyte unterliegt hohen technischen Anforderungen, um eine hohe Produktionsausbeute und stabile Qualität zu erreichen.
Die Qualität, d. h. die strukturelle Integrität der keramischen Elektrolyte bestimmt die Leistung und Lebensdauer der Batteriezelle. Die Überwachung des Zustands der keramischen Elektrolyte in der anfänglichen Produktionsphase hilft dabei, defekte Komponenten rechtzeitig zu erkennen und auszusortieren. Bisher angewendete manuelle und visuelle Qualitätskontrollen, wie die optische Inspektion mit Kaltlicht oder He-Leckage Messungen sind nicht inline-fähig und vor allem nicht für große Produktionskapazitäten geeignet.
Sensor erkennt kleinste Defekte im Elektrolyten
Im BMBF-geförderten Projekt InBatt soll daher ein optoelektronischer LSP-Sensor zur Erkennung von Herstellungsdefekten für Na-ß"-Aluminiumoxid-Elektrolyte im nicht-gesinterten Zustand entwickelt und qualifiziert werden. Dieser basiert auf der Laser-Speckle-Photometrie (LSP). Diese Messmethode ist hinsichtlich kleiner Defektgrößen extrem sensitiv. So hat die LSP das Potenzial, typische Fehler, wie mikroskopisch kleine Poren, Mikrorisse, Rauheitsstrukturen und lokale Inhomogenitäten der Materialzusammensetzung zu detektieren.
100%-Prüfung in Echtzeit vor dem Sintern
Die LSP prüft die entstehende Struktur bzw. den noch ungesinterten Elektrolyten hundertprozentig auf Fehler. So kann der energieintensive Sinterprozess geschädigter Elektrolyte vermieden werden. Das Material der noch nicht gesinterten und fehlerhaften Elektrolyte soll perspektivisch im Kreislauf geführt werden und für die Herstellung neuer Elektrolyte Verwendung finden.
Die Selektion fehlerhafter Elektrolyte erfolgt berührungslos und in Echtzeit. Die 100 %-Prüfung erzeugt Bilddaten, die zur Bewertung der Elektrolytqualität digital ausgewertet werden. Dadurch soll der Ausschuss in der Batteriezellproduktion weiter gesenkt werden.
Zum Ende des Projektzeitraums wird ein Technologiedemonstrator realisiert und in ein Fertigungstechnikum integriert sein.
Über das Projekt
Die BMBF-Förderrichtlinie CGoIn fördert das Projekt InBatt (Förderkennzeichen 03XP0644) mit etwa 2,5 Mio. Euro. Das Vorhaben startet am 1.1.2025 und läuft über drei Jahre. Das Konsortium besteht aus der Automation Uhr GmbH (Projektkoordinator), GÖPEL electronic GmbH, ECT-KEMA GmbH sowie dem Fraunhofer-Institut für Keramische Technologien und Systeme IKTS mit seinen Standorten in Hermsdorf/Thüringen und Dresden-Klotzsche.
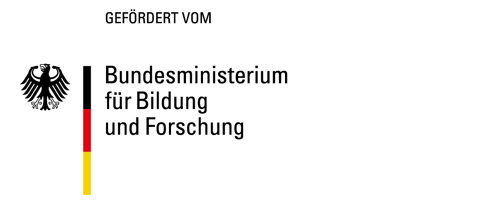