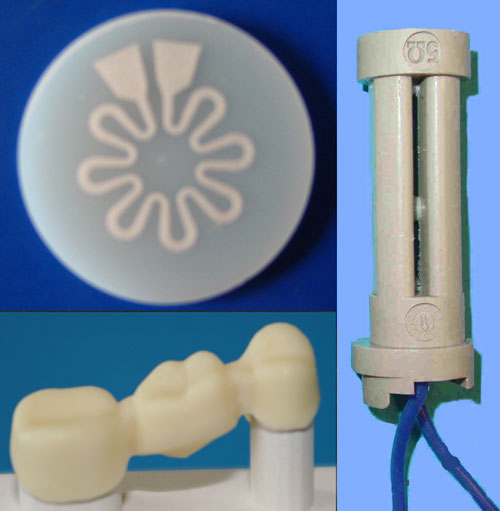
Ceramic and polymer-ceramic Components: Sensor element (left top), Highl power starting resistor (right), ZrO2 bridge frameworks(left below).
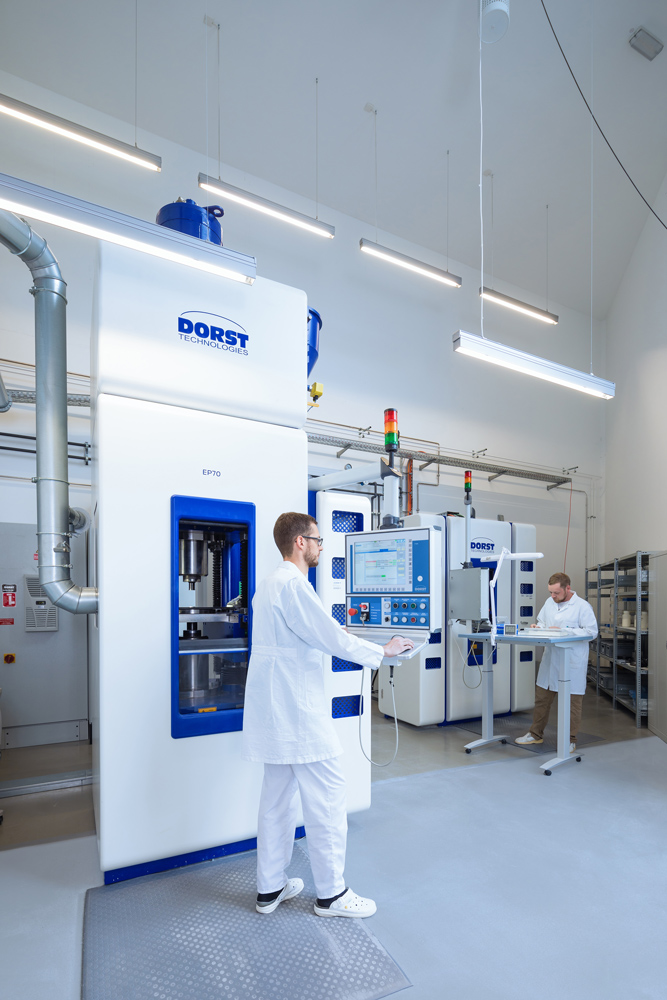
Servo-motorized CNC press.
Profile
- Oxide ceramic materials with high density, purity, strength and functional dopants for customized applications using superfine starting powders
- Ceramic materials with homogeneous,poor in defects and superfine structure design
- Optoceramic materials for Photonic Technologies
- Bioceramic and glass-ceramics for dental and surgical implants
- Ceramic-like composites (polymer ceramics) based on pre-ceramic silicone polymers with an advantageous combination of ceramic-like and plastics-like properties
- Development of industry-oriented manufacturing technologies with the inclusion of modern production technologies to assure custom-designed structur-property-relation
Services offered
- Development of single and multi-phase oxid ceramic components for special applications(mean system is Al2O3-ZrO2-MgO-Y2O3-SiO2)
- Polymer ceramics with fiber reinforcement and functional filling (electrical , thermal , and dielectric conductivity)
- Prototype- and small series manufacturing according customer specification
- Manufacturing technologies to avoid flaws for advanced properties
- Development of ready- to- press granules
- Uniaxial dry pressing for samples
- Slip casting of ceramic components with complex geometry
- CAD/CAM-process chain for manufacturing for instance dental restorations
- Manufacture of material composites combining ceramics and metals or polymer ceramics, ceramics, and metals
- Plastic forming of plastics and thermo-set materials (injection moulding, extrusion, warm pressing)
Technical equipment
- Ultra fine milling from sub-µm- to nm-range
- Spray dryers in laboratory
- Uniaxial dry pressing (mechanical and hydraulic)
- Shear roll for manufacture of granulates
- Scanner/4-axis-CNC-milling machines
- High pressure injection moulding equipment
- Thermal processes (reductive and oxidic)
- Final machining ( precision grinding and lapping)
- Measuring mixers and rheometers for determination of flow properties of high viscous and reactive materials