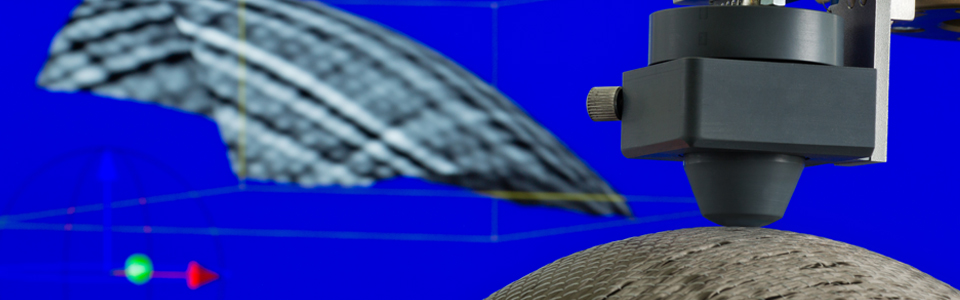
Industry 4.0 and big data methods will lead to a paradigm shift in the application of non-destructive components testing and materials diagnostics methods. These methods are an essential source of valuable data. New sensor concepts, robot-assisted measurements, cloud-based data acquisition, and data evaluation using AI methods are driving this transformation and expanding the application range of new and well-established NDT methods.
Backed by several decades of experience, Fraunhofer IKTS and its Materials Diagnostics Division are positioned to cope with these challenges. IKTS concepts established in ceramics development – covering complete value chains and realizing material and process innovations at the system level – can also be transferred to materials diagnostics. Non-destructive components testing (NDT) and materials diagnostics will be performed over the entire product life cycle, from development to testing or monitoring in production and use. For this, Fraunhofer IKTS draws on traditional methods such as ultrasonic, eddy current, and x-ray inspection as well as acoustic diagnostics, combining or supplementing these techniques with new methods such as laser speckle photometry or optical coherence tomography. By linking the data acquired during testing with a dynamic simulation model of the part or system, it is possible to predict the service life or performance with the help of the “digital twin”.
Fraunhofer IKTS is part of the globally leading Dresden Materials Research Cluster and cooperates with the Dresden Microelectronics Network as well as various established mechanical engineering companies.
Innovation and development are the cornerstones of a promising corporate future. In order to create a competitive edge, Fraunhofer offers tailored options for cooperation, so that small and medium-sized companies can work together in the best possible way. This also allows to utilize development skills at short notice and as needed.