Author: Maria Kaminski
#diensttalk with Sebastian Stark aubout Prototyping: Virtual optimization of piezo system solutions
Piezo system solutions are suitable for a variety of sensory applications in the field of medical technology, ultrasonic generation or even in non-destructive material testing. The manufacturing process is complex and can lead to destruction of the component in case of unsuitable component design or errors in the poling process. For this reason, Fraunhofer IKTS specializes in various prototyping processes: The advantage: time and resources are reduced to a minimum by computer-aided methods, while at the same time optimizing the product properties.
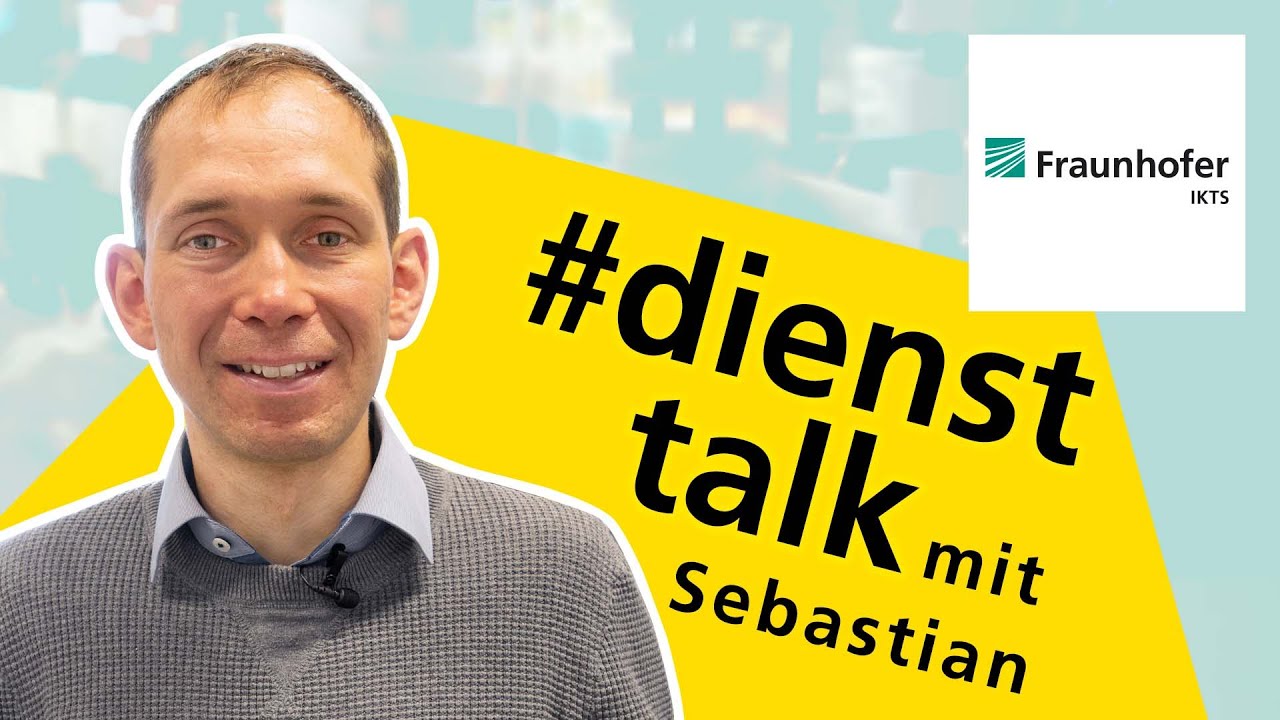
Privacy warning
With the click on the play button an external video from www.youtube.com is loaded and started. Your data is possible transferred and stored to third party. Do not start the video if you disagree. Find more about the youtube privacy statement under the following link: https://policies.google.com/privacyThe #diensttalk with Sebastian Stark: In the #diensttalk, employees give a little insight behind the scenes of Fraunhofer IKTS and reveal what drives them in their research.
Stay informed: Feel free to sign up for our newsletter, check out other blog posts, or follow us on Facebook, Instagram, LinkedIn, YouTube and Twitter. We look forward to getting in touch with you. (Video in German)
Everyone has used it at least once: A lighter. What few people know is that in many lighters the ignition spark is generated by a so-called piezoelectric material. The pressure load on the piezoelectric element causes a displacement of electrical charges and thus the formation of a spark. This phenomenon is also known as the piezoelectric effect, which can be found in a variety of other applications. For example, it is used for ultrasound generation in medical technology, for cleaning contaminated components, in non-destructive materials testing and also for fuel injection in internal combustion engines.
In addition to these classic applications, new fields of application are constantly being added: For example, extensive research is being conducted into using piezo elements in the treatment and analysis of wastewater to accelerate chemical reactions. Opening up new areas of application requires the development of complex designs to meet the requirements.
Dr. Sebastian Stark heads the Applied Material Mechanics and Solid-State Transducers group. His place of work: Fraunhofer IKTS in Dresden. His vision: a prototype-free, completely virtual design of piezo systems. We asked how he would like to realize his vision at Fraunhofer IKTS.
How are piezoelectric elements manufactured?
Various processes are used to shape piezoelectric ceramics, such as pressing, tape casting or thick-film technology. The subsequent sintering is followed by the so-called poling process. In this process, a preferred direction is introduced into the material by applying a high electric field, so that the coupling of electrical and mechanical properties that exists at the microscopic level also takes effect at the component level. The poling determines the piezoelectric properties of the component. During the poling process, complex, strongly nonlinear effects occur, which can lead to destruction of the component if the component design or poling process is unsuitable. For this reason, a time-consuming and costly iterative trial-and-error process is often required for the optimal design and manufacture of piezoelectric ceramic components and assemblies. This process can be made much more efficient with computer-aided methods, such as the finite element method (FEM). This can simulate the poling process and predict the resulting piezoelectric properties of the component by numerically solving the continuum mechanical equations describing the poling process. To do this, the component of interest is decomposed into a large number of smaller, geometrically simple elements (e.g. tetrahedra). Within these, the solution for the quantities of interest can be approximated by simple mathematical functions. By combining the solutions of the individual “finite” elements, an approximate solution for the overall problem is finally obtained. The great advantage of the FEM over other methods is that in particular complex shaped components can be calculated.
How does the simulation-based design process work?
The starting point for simulation-based design is typically a parametric CAD model of the component. By varying geometric parameters and the materials used, a multitude of possible realizations of the component results. It is not obvious from the outset which of the realizations is best suited for the intended use in terms of function and cost. Therefore, the poling process is simulated for these realizations using the method described. The results are evaluated according to predefined criteria, such as the extent of electromechanical coupling. Based on this, the optimal solution is finally selected.
What are the advantages of the finite element method (FEM)?
In the classical iterative approach, a large number of prototypes are produced and extensively tested. With the FEM method, on the other hand, the behavior of the prototypes during the poling process and the resulting piezoelectric properties can be virtually implemented and investigated. In addition, more parameter combinations and more complex geometries can be considered. This can drastically reduce the number of necessary prototypes, development times and costs, which in turn conserves resources.
The core of the simulation methodology is the underlying material model of the piezoceramic material. This describes the material behavior mathematically and forms the basis for the FEM simulations. A number of material parameters occur in the material model that must be identified experimentally. Both the development of the material models and the material parameter identification represent key competences of Fraunhofer IKTS. The material models are implemented using modern programming languages and environments and are linked to commercial finite element software packages such as ANSYS or Comsol. With the help of these, the simulations described are carried out at component level, with the material parameters required for this being determined on various test rigs, some of which have been specially developed for this purpose.
What can the simulation method be used for?
One example of application is the poling of piezoelectric fibers in active-fiber composites, which are used either as sensors or actuators to monitor and influence the condition of structures. Notch electrodes are used to realize the required electric fields to enable the necessary poling of the fibers in the longitudinal direction. In this context, the simulation method can determine the ideal notch electrode depth. Other experiments are thus no longer required. In addition, further parameter studies regarding the shape of the notch base can be realized to further increase the electromechanical coupling of the active-fiber composite available after the poling process.
What do you wish for the future?
My main goal for the future is to minimize the time and resources required by developing computer-aided methods while optimizing the product properties. In particular, the existing material models for piezoelectric ceramics and the associated experiments for material parameter identification must be further developed. This concerns the increase of the prediction quality of the models as well as the transfer to new, partly lead-free materials, as well as the reduction of the effort for the material parameter identification. Another promising approach is the coupling of the simulation method to mathematical shape optimization methods, which offer the possibility to automatically adapt the component shape with regard to the optimization of certain properties.

Here you can find more #diensttalks. Take a look behind the scenes of Fraunhofer IKTS.
Also stay informed: You are welcome to subscribe to our newsletter, read our other blog articles and follow us on LinkedIn, Instagram and YouTube.