Cost-effective wind energy thanks to automated maintenance
The expansion of onshore wind turbines is stagnating. This is mainly due to rarely suitable areas and protests by residents. Wind turbines on the open sea are an alternative – but the production of offshore energy is currently much more expensive. This is also due to the higher maintenance costs. Fraunhofer IKTS has developed a measuring system that is permanently installed on the foundation structure of offshore plants to permanently monitor it. This reduces the effort required for cost-intensive on-site operations and thus the mainte-nance costs.
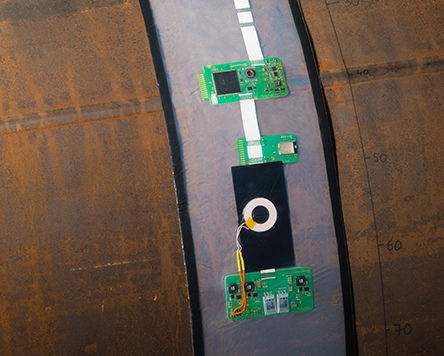
In 2018, a kilowatt hour of wind power generated at sea cost an average of eleven cents, almost twice as much as one generated onshore. Maintenance costs are among the biggest cost drivers. The law requires that at least 25 percent of the turbines in a wind farm are serviced each year. For example, every wind turbine must be checked every four years in purely mathematical terms. Above all, testing the metal fixations on the seabed, the so-called foundation structures, is complex and dangerous.
Avoiding risky and expensive on-site operations
For maintenance, technicians and material must be brought to the plant by ships. The prerequisite for transport and the necessary underwater operations are suitable weather conditions, which are only actually present on a few days a year. In addition, the costs for ship rental and diving are very high. With a sensor ring developed at Fraunhofer IKTS, these costs can be significantly reduced.
Like a ring, the sensors are attached directly and permanently to heavily loaded areas of foundation structures, such as welded seams. This means that externally growing biomaterial has far less influence on the measurements and that the strenuous and time-consuming manual cleaning of the measuring points by divers is no longer necessary.
Sensors are integrated into the ring and act alternately as sensor or actuator. This means that they are able to transmit or receive special ultrasonic waves. The reflection pattern of these waves in the material allows damage, such as weld cracks, to be detected.
Robust sensor technology for underwater use
In addition to biomaterial, corrosive salt water and the enormous forces of the waves also become a problem for the sensory measuring systems. Dr. Bianca Weihnacht, scientist at Fraunhofer IKTS, explains the challenges: “In order to be able to measure permanently under water, the sensor ring must withstand the harsh environmental conditions. For this reason, the sensors are protected against seawater by several laminated barrier layers. However, this only works with flat electronic components that we had to develop. For example, flat coils for energy transmission are integrated into the sensor ring“.
Wireless energy and data transmission
The readout of the measured data at the sensor ring is no longer carried out by divers, but by “Remote Operating Vehicle“ (ROV) – underwater robots that are remote-controlled via cable. The measured data is transferred from the sensor ring to the diagnostic device on the robot via WLAN, and then via the cable to the technicians on the ship. In future, this work step will also be optimized by wirelessly transmitting both the measurement data and the required energy over long distances from the sensor ring to the maintenance station. “By means of the sensor ring, we actively contribute to increase operating safety and reduce the maintenance costs of offshore wind turbines“ summarizes Bianca Weihnacht.
Intelligent maintenance concepts such as the sensor ring will make wind power even more attractive. This brings the federal government's great goal for 2030 within reach: The share of renewable energies in the electricity mix is to rise to 65 percent – a large proportion of which will be wind energy.